Application field
1. Uninterruptible power supply 2. Photovoltaic inverter 3. Server power 4. DC charging pile 5. New energy vehicles 6. Air conditionerPerformance Characteristics
· Has a uniformly distributed air gap ·High saturation magnetic flux density (1.2T) ·Low loss · Low magnetostriction coefficient · Stable temperature and frequency characteristicsCraftsmanship
Sendust core are formed by adding a certain amount of glass forming agent to the molten metal, and rapidly quenching and casting using a narrow ceramic nozzle under high temperature melting conditions. Amorphous alloys have the similar characteristics of glass structure, which not only make them have excellent mechanical properties, physical properties and chemical properties, but more importantly, the new technology of producing amorphous alloys using this rapid quenching method is less than the cold-rolled silicon steel sheet process. 6 to 8 processes can save energy consumption by 60% to 80%, which is an energy-saving, time-saving and efficient metallurgical method. Moreover, the amorphous alloy has low coercivity and high magnetic permeability, and its core loss is significantly lower than that of oriented cold-rolled silicon steel sheet, and its no-load loss can be reduced by about 75%. Therefore, the use of amorphous alloys instead of silicon steel sheets to manufacture transformer cores is one of the main means to save energy and reduce consumption in today's power grid equipment.Parameter Curve
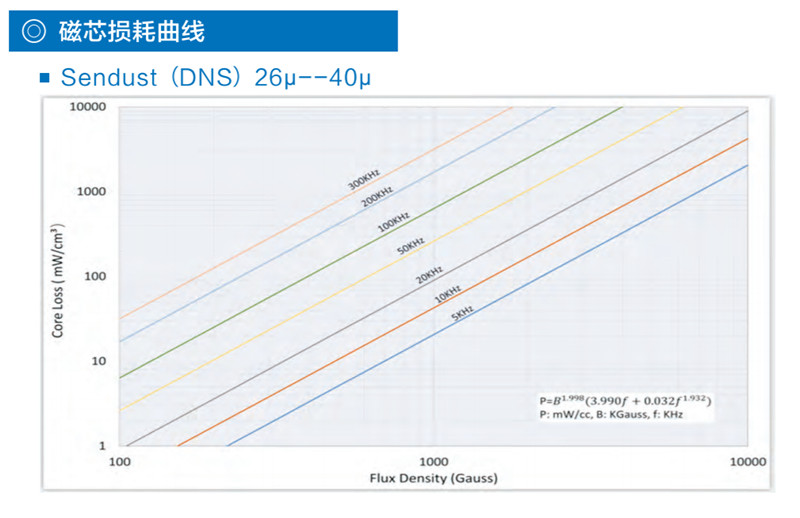
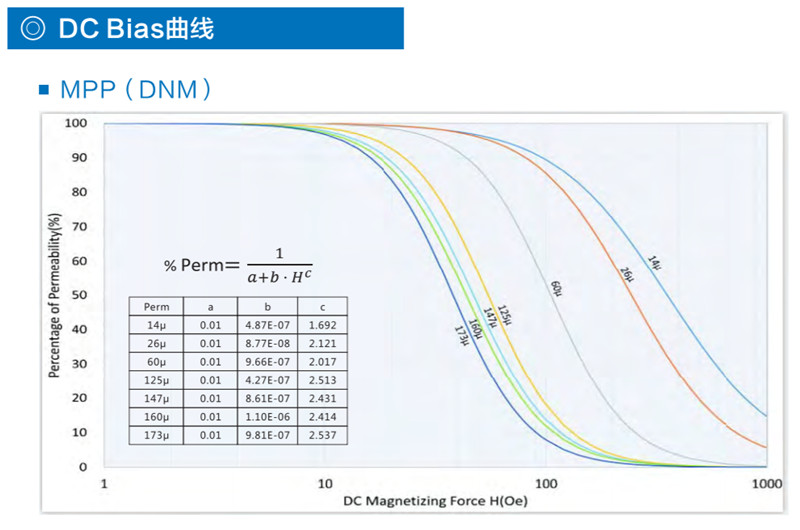
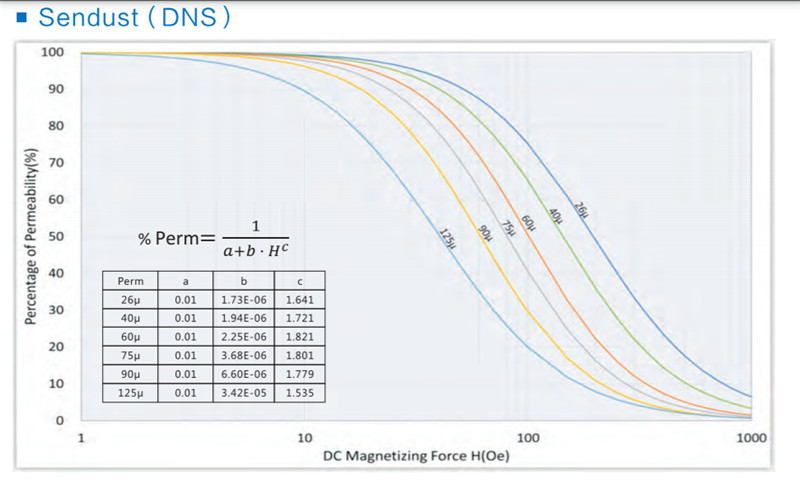
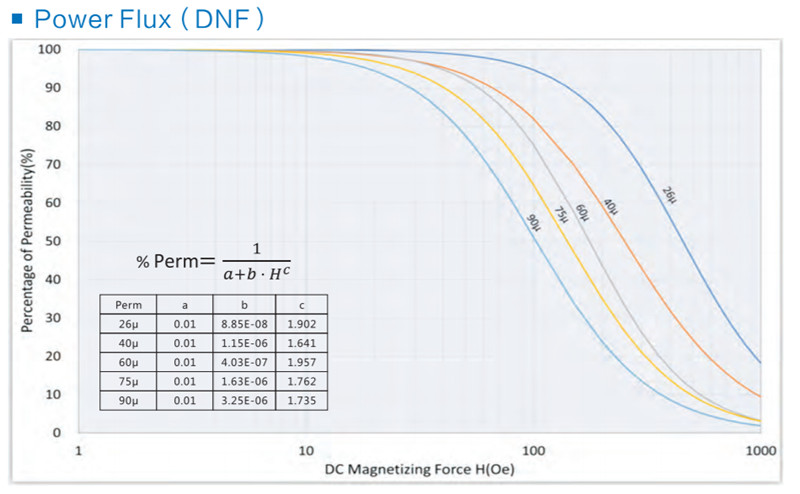
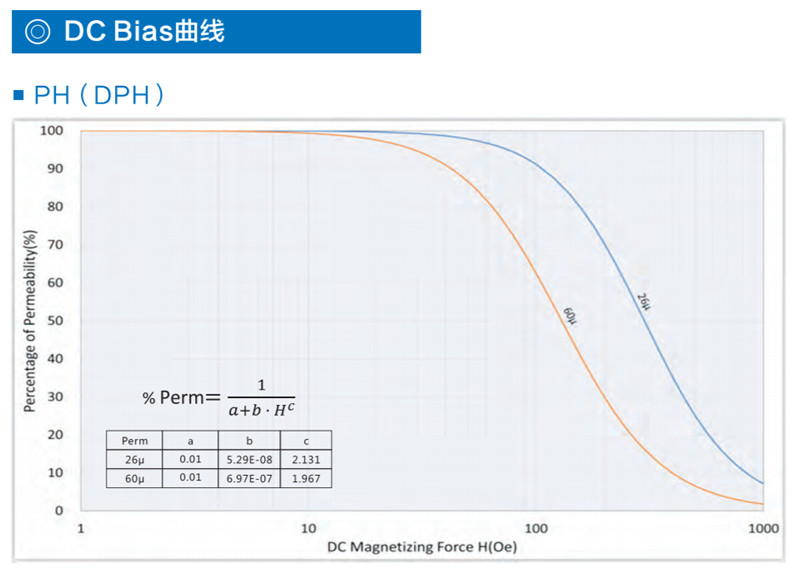
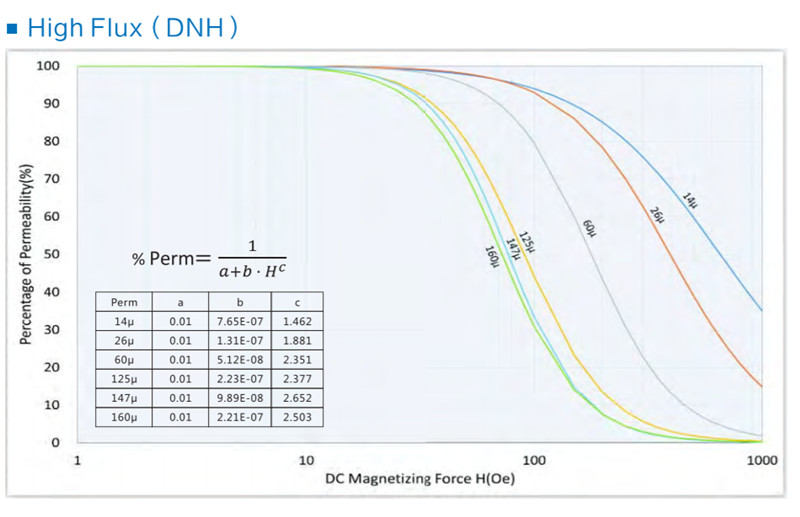
Introduction
This application guide presents some general guidelines for the optimum choice of powder core materials ( MPP, Sendust, Kool Mu®, High Flux or Iron Powder ) for different inductor, choke and filter design requirements. The choice of one type of material over another often depends on the following: 1) DC Bias Current through the inductor 2) Ambient Operating Temperature and acceptable temperature rise. Ambient temperature of over 100 deg C is now quite common. 3) Size constraint and mounting methods ( through hole or surface mount ) 4) Costs : iron Powder being the cheapest and MPP, the most expansive. 5) Electrical stability of the core with temperature changes 6) Availability of the core material. For example, Micrometals #26 and #52 are mainly available from stock. Most commonly available MPP cores is the 125 permeability materials, etc. As a result of recent advances in ferromagnetic technology, a greater choice of core materials for design optimization is now available. For switch mode power supplies (SMPS), inductors, chokes and filters, typical materials are MPP (molypermalloy powder), High Flux , Sendust, and Iron Powder cores. Each of the above power core materials has individual characteristics suitable for different applications. The common manufacturers of the above powder cores are: 1) Micrometals for iron powder cores. Only Micrometals cores are tested for thermal stability and CWS only uses Micrometals cores in all its designs. 2) Magnetics Inc, Arnold Engineering, CSC, and T/T Electronics for MPP, Sendust ( Kool Mu®), and High Flux cores 3) TDK, Tokin, Toho for Sendust Cores With powder cores, high permeability material is ground or atomized into powder. The permeability of the cores will depend on the particle size and density of the high permeability materials. Adjustment of the particle size and density of this material leads to different permeability of the cores. The smaller the particle size, the lower the permeability and better DC bias characteristics, but at a higher cost. The individual powder particles are insulated from one another, allowing the cores to have inherently distributed air gaps for energy storage in an inductor. This distributed air gap property ensures that the energy are stored evenly through the core. This makes the core have a better temperature stability. Gapped or slitted ferrites stores the energy in the localized air gap but with much more flux leakage causing localized gap loss and interference. In some cases, this loss due to localized gap can exceed the core loss itself. Due to the localized nature of the air gap in a gapped ferrite core, it does not exhibit good temperature stability. Optimum core selection is to choose the best material with a minimal compromise while meeting all design objectives. If cost is the primary factor, iron powder is the choice. If temperature stability is the primary concern, MPP will be the first option. The attributes of each type of material are discussed briefly. All the 3 types of powder cores can be purchased on-line in small volume from stock (immediate delivery) at the following website: www.cwsbytemark.com. More technical data of these materials can be found in www.bytemark.com MPP (Molypermalloy Powder Cores) Composition: Mo-Ni-Fe MPP cores has the lowest overall core loss and best temperature stability. Typically, inductance variance is under 1% up to 140 deg C. MPP cores are available in initial permeabilities (µi) of 26, 60, 125, 160, 173, 200, and 550. MPP offers high resistivity, low hysteresis and eddy current losses, and very good inductance stability under DC bias and AC conditions. Under AC excitation, inductance change is under 2% (very stable) for µi=125 cores at AC flux density of over 2000 gauss. It does not saturate easily at high DC magnetization or DC bias condition.The saturation flux density of MPP core is approximately 8000 gauss ( 800 mT) Compared to other materials, MPP cores are the costliest, but highest quality in terms of core loss and stability. For application involving DC bias condition, use the following guidelines. To get less than 20% decrease in initial permeability under DC bias condition:- For µi= 60 cores, max. DC bias < 50 oersted; µi=125, max. DC bias < 30 oersted; µi=160, max. DC bias <20 oersted.Unique Features
1.Lowest core loss among all the powder materials. Low hysteristics loss resulting in low signal distortion and low residual loss. 2.Best temperature stability. Under 1%. 3.The maximum saturation flux density is 8000 gauss (0.8 tesla) 4.Inductance tolerance: + - 8%. (3% from 500 Hz to 200 Khz) 5.Most commonly used in aerospace, military, medical and high temperature application. 6.Most readily available as comapred to high flux and sendust. Applications : High Q filters, loading coils, resonant circuits, RFI filters for frequencies below 300 kHz, transformers, chokes, differential mode filters, and DC biased output filters. High Flux Cores Composition: Ni-Fe High Flux cores is composed of compacted 50% nickel and 50% iron alloy powder. The base material is similar to the regular nickel iron lamination in tape wound cores. High Flux cores have higher energy storage capabilities, and higher saturation flux density. Their saturation flux density is around 15,000 gauss ( 1500 mT), about the same as iron powder cores. High Flux cores offers slightly lower core loss than Sendust. However, High Flux's core loss is quite a bit higher than MPP cores. High Flux cores are most commonly used in application where the DC bias current is high. However, it is not as readily available as MPP or Sendust, and are limited in its permeability choices or size selections. Applications : 1) In Line Noise filters where the inductor must support large AC voltages without saturation. 2) Switching Regulators Inductors to handle large amount of DC bias current 3) Pulse Transformers and Flyback Transformers as its residual flux density is near to zero gauss. With the saturation flux density of 15K gauss, the usable flux density ( from zero to 15K gauss) is ideally suited for unipolar drive applications such as pulse transformer and flyback transformers. Kool Mu® / SENDUST Composition: Al-Si-Fe Sendust cores are also known as Kool Mu® from Magnetics Inc., Sendust material was first used in Japan in an area called Sendai, and it was called the 'dust' core, and thus the name Sendust. In general, sendust cores have significantly lower losses than iron powder cores, but have higher core losses than MPP cores. Compared to iron powder, sendust core loss could be as low as 40% to 50% of Iron powder core loss. Sendust cores also exhibits very low magnetostriction coefficient, and it is therefore suitable for applications requiring low audible noise. Sendust cores has a saturation flux density of 10,000 gauss which is lower than Iron powder. However, sendust offers higher energy storage than MPP or gapped ferrites. Sendust cores are available in initial permeabilities (Ui) of 60 and 125. Sendust core offer minimal change in permeability or inductance (under 3% for ui=125) under AC excitation. Temperature stability is very good at the high end. Inductance change is less than 3% from ambient to 125 deg C. However, as the temperature decreases to 65 deg C, its inductance decreases by about 15% for µi=125. Also note that as temperature increases, sendust exhibits a decrease in inductance versus an increase in inductance for all the other powder materials. This could be a good choice for temperature compensation, when used with other materials in a composite core structure. Sendust cores cost less than MPPs or high fluxes, but slightly more expensive than iron powder cores. For application involving DC bias conditions, use the following guidelines. To get under 20% decrease in initial permeability under DC bias condition: For µi= 60 cores, max. DC bias < 40 oersted; µi=125, max. DC bias < 15 oersted.Unique Features
1.Lower core loss than Iron Powder. 2.Low magnetostriction coefficient, low audible noise. 3.Good temperature stability. Under 4% from -15 'C to 125 'C 4.Maximum flux density: 10,000 gauss (1.0 tesla) 5.Inductance tolerance: ±8%. Applications: 1.Switching regulators or Power Inductors in SMPS 2.Fly-back and Pulse transformers (inductors) 3.In-Line noise filters 4.Swing chokes 5.Phase control circuits (low audible noise) light dimmers, motor speed control devices. Iron Powder Composition: Fe Iron powder is the most cost effective of all the powder cores. It offers a cost effective design alternative to MPP, High Flux or Sendust cores. Its higher core loss among all the powder materials can be compensated by using bigger size cores. In many applications, where space and higher temperature rise in the iron powder cores are insignificant compared to savings in costs, iron powder cores offers the best solution. Iron Powder cores are available in 2 classes : carbonyl iron and hydrogen reduced iron. Carbonyl iron has lower core losses and exhibits high Q for RF applications. Iron Powder cores are available in permeabilities from 1 to 100. The popular materials for SMPS applications are #26 (µi=75), #8/90 (µi=35), #52 (µi= 75) and #18 (µi=55). Iron powder cores have saturation flux density of 10,000 to 15,000 gauss. Iron powder cores are quite stable with temperature. The #26 material has temperature stability of 825 ppm/C (inductance change of approximately 9% with temperature change of up to l25 deg C).The#52 material is 650 PPM/C (7%). The #18 material is 385 PPM/ C (4%), and the #8/90 material is 255 PPM/C (3%). Iron powder cores are ideal in lower frequency applications. Since their hysteresis and eddy current core loss are higher, the operating temperature should be limited to below 125 deg C. For application involving DC bias conditions, the following guidelines are recommended. To get under 20% decrease in initial permeability under DC bias condition: For Material #26, max DC bias < 20 oersteds; For Material #52, max DC bias < 25 oersteds; For Material #18, max DC bias < 40 oersteds; For Material #8/90, max DC bias < 80 oersteds.Unique Features
1.Lowest costs. 2.Good for low frequency application (<10OKhz). 3.High maximum flux density: 15,000 gauss 4.Inductance tolerance ± 10% Applications: 1.Energy storage inductor 2.Low frequency DC output chokes 3.60 Hz differential mode EMI Line Chokes 4.Light Dimmers Chokes 5.Power Factor correction Chokes. 6.Resonant Inductors. 7.Pulse and Fly-backTransformers 8.In-line noise filters. Able to withstand large AC line current without saturation. DC Biased Inductor Operation. 20% Permeability LimitsMaterials | Initial Perm. | Max. DC Bias (Oersteds) |
MPP | 60 125 160 | < 50 < 30 < 20 |
High Flux | 60 125 | < 45 < 22 |
Sendust | 60 125 | < 40 < 15 |
Iron Powder Mix #26 Mix #52 Mix #18 Mix #8/90 | 75 75 55 35 | < 20 < 25 < 40 < 80 |
Materials | Relative Cost |
Iron Powder Mix#26 Mix#52 Mix#18 Mix#8/90 | 1.0 1.2 3.0 4.0 |
Sendust | 3.0 to 5.0 |
High Flux | 7.0 to 10.0 |
MPP | 8.0 to 10.0 |
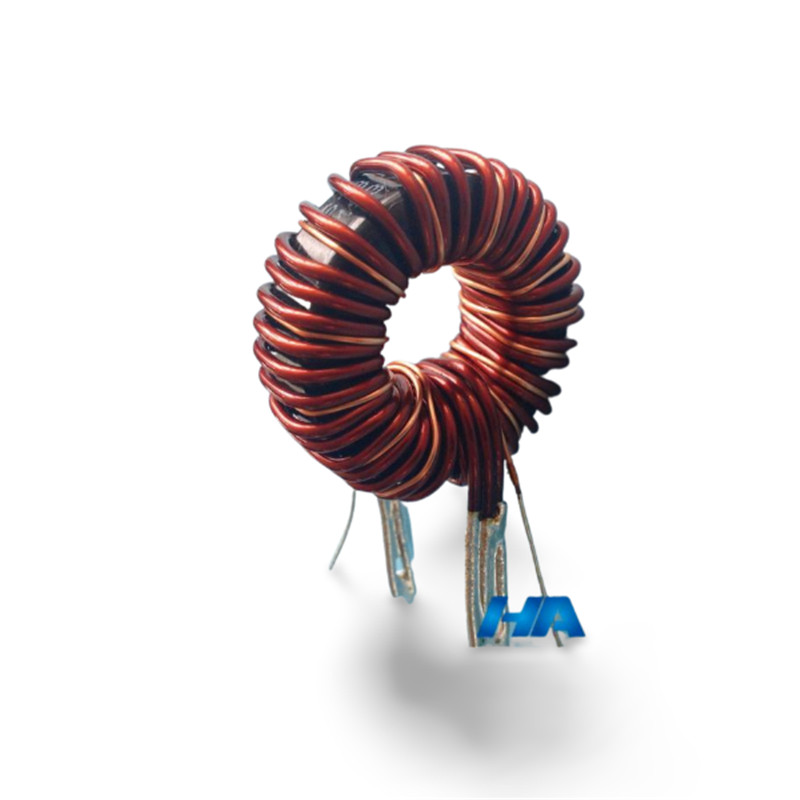
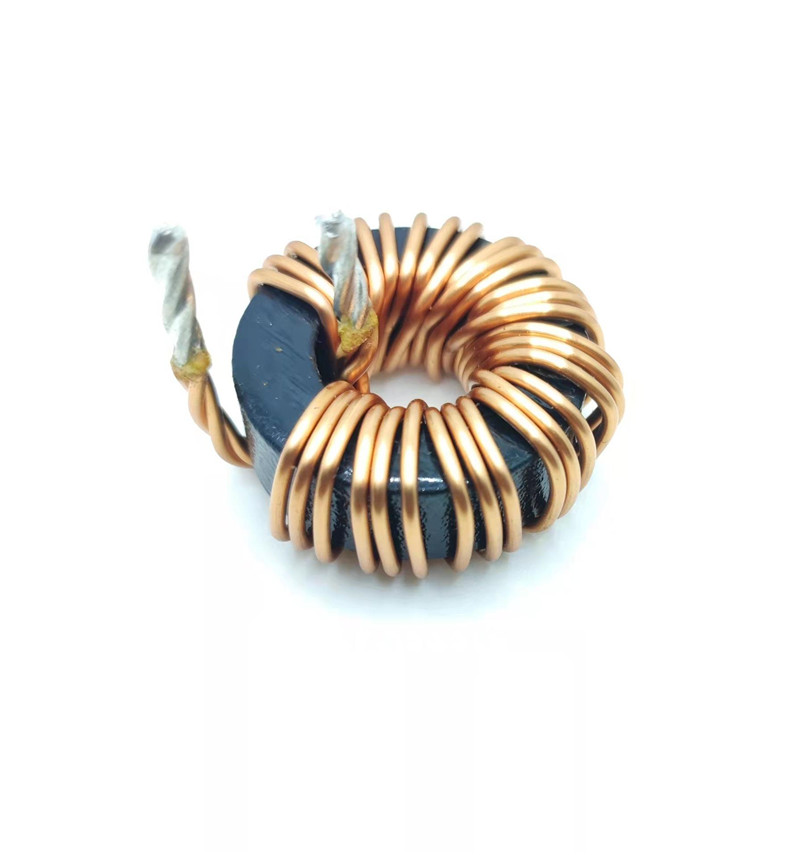