Inverter welding machines have become increasingly popular in recent years due to their advanced technology and efficiency in various welding applications. These machines use a power source that produces high-frequency alternating current to weld metals of different thicknesses, thus providing a high-quality weld. The inverter welding machines also come with advanced features such as multi-mode capability, synergic control, and MMA/TIG welding, making them versatile in various industrial applications.
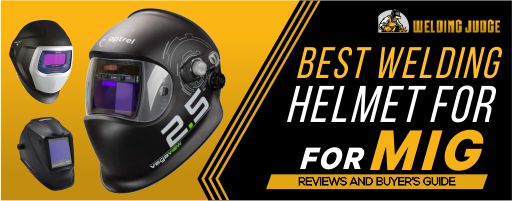
One of the essential features of inverter welding machines is their core function, which is to provide a stable, consistent current to the welding process. In contrast to conventional transformers, inverter welding machines utilize high-frequency electronic switching to generate the necessary output current. This technology allows for a reduction in weight and size of the machine while increasing the efficiency and overall performance.
Multi-Mode Capability
Inverter welding machines, such as the XTM 252I synergic MIG inverter package, have the capability of welding up to 8mm thick material. The multi-mode capability enables these machines to be used for different welding applications in various industries such as automotive repair, metal fabrication, and manufacturing. This feature is particularly beneficial for small-scale operations that require versatile machines that can carry out different welding tasks.
Synergic Control
The synergic control feature is another essential function of inverter welding machines. It allows for rapid set-up of the welding process and ensures consistency in the weld quality. Synergic control simplifies the task of finding the right welding parameter as it selects the optimal setting based on the wire type, thickness, and material, allowing even beginners to produce high-quality welds. It also reduces the chances of having spatter, a common issue in MIG welding, which can result in an unsightly finish.
MMA and TIG Welding
Another advantage of inverter welding machines is their ability to carry out other welding techniques like TIG and MMA. The versatility of these machines opens up various welding applications, allowing users to work on different types and thicknesses of metals. While MIG welding is commonly used in manufacturing and metal fabrication, TIG welding is often utilized in repair works, particularly in sectors like aerospace and transportation. MMA welding, on the other hand, is commonly used in construction and maintenance, where portability is essential.
Reliable Feeding
Inverter welding machines are equipped with a 4-roll geared aluminum feed box, ensuring reliable feeding of wires of different thicknesses. The feed box eliminates wire slippage and tangling while ensuring that the wire is fed uniformly throughout the welding process. This feature is particularly important in metal fabrication, where a seamless weld is essential in the final product.
Portability
Lastly, inverter welding machines are often designed with portability in mind. The XTM 252I, for example, has large wheels that make it easy to move from job to job. The machine's full-size cabinet can also accept a full-height gas cylinder, ensuring that the machine's components are secure during transport.
Conclusion
In conclusion, inverter welding machines offer core functions, including stable, consistent current, multi-mode capability, synergic control, MMA/TIG welding, reliable wire feeding, and portability. These features make these machines suitable for various welding applications and industries where efficiency and versatility are essential. As the demand for advanced welding technology continues to grow, inverter welding machines will remain at the forefront of technological innovation in the welding industry.