Inductors and chokes are some of the essential components in electronics, particularly in power supply systems. They are responsible for storing and releasing energy when needed and are widely used in various applications such as switch-mode power supplies, inverter circuits, and more. The market for inductor and choke production has become more competitive due to the increasing demand for better performance, higher reliability, and lower cost. Fortunately, King Magnetics has introduced a new type of core that can help manufacturers achieve these goals – the Amorphous and Nanocrystalline Gap Cores.
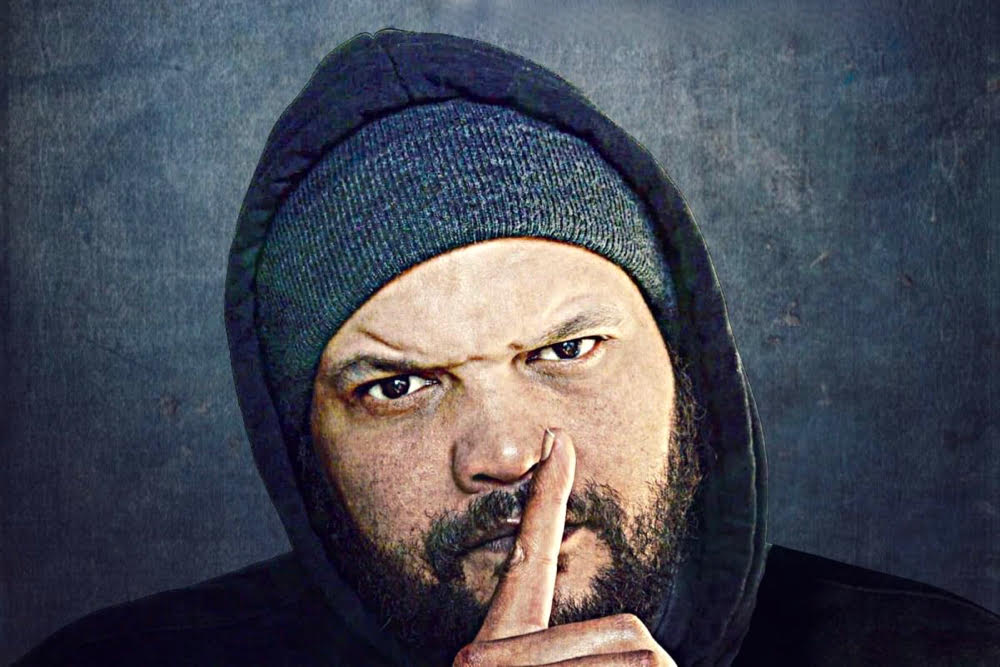
What is an Amorphous Gap Core?
An Amorphous Gap Core is a type of core that is made from an amorphous alloy. This alloy is produced by rapid cooling, which prevents the formation of a crystalline structure. The resulting material has a disordered atomic structure, which gives it unique magnetic properties. In comparison to other types of cores, amorphous cores have higher saturation flux density, which means they can store more energy in a smaller size. Additionally, amorphous cores have low core loss and high permeability, making them ideal for use in high-frequency applications.
What is a Nanocrystalline Gap Core?
Like amorphous cores, Nanocrystalline Gap Cores are made from metal alloys. However, nanocrystalline cores contain small crystalline particles that are dispersed within an amorphous matrix. This unique structure gives nanocrystalline cores a combination of high magnetic permeability and low coercivity, which makes them ideal for use in high-frequency applications. The nanocrystalline structure also makes them more resistant to thermal demagnetization, providing them with greater stability and reliability over long periods.
The Advantages of Amorphous and Nanocrystalline Gap Cores
The combination of amorphous and nanocrystalline materials creates a core that has the advantages of both types of materials. These advantages can be summarized as follows:
- High saturation flux density – Amorphous and nanocrystalline cores have a high saturation flux density that allows them to store more energy in a smaller size.
- Low core loss – The unique magnetic properties of amorphous and nanocrystalline cores give them low hysteresis and eddy current losses, making them more energy efficient.
- High permeability – Amorphous and nanocrystalline cores have high permeability, which allows for better coupling between coils and results in better inductance.
- Low cost – Compared to High Flux cores, amorphous and nanocrystalline cores are more cost-effective, making them an excellent alternative.
Applications of Amorphous and Nanocrystalline Gap Cores
Amorphous and Nanocrystalline Gap Cores are suitable for many applications that require high-performance inductors and chokes. Some of these applications include:
- Hall-effect sensor concentrators
- Output inductors
- Power factor correction chokes
- Differential mode chokes
Since these components are crucial in electronics applications in aerospace, medical, and automotive industries, choosing the right components with excellent performance and low cost is crucial for the success of the project. With the use of Amorphous and Nanocrystalline Gap Cores, manufacturers can achieve better performance, reliability, and cost-effectiveness in their products, which will ultimately benefit consumers.
In conclusion, the introduction of Amorphous and Nanocrystalline Gap Cores by King Magnetics is a significant development in the inductor and choke industry. These cores provide immense advantages such as high saturation flux density, low core loss, high permeability, and low cost. As these materials become more widely adopted in the industry, we can expect to see increased use of these cores in various applications requiring high-performance components – making their production a natural evolution in the market.